Product
HOME/PRODUCTS/HOUSINGLESS MILLS
High rigidity, reliability and quick roll change capabilities are the key features of the state of the art mill stands, which are designed for producing bars, wire rod, angles, channels, and universal beams. The connection and disconnection of the spindles and all the fluid utilities are fully automatic and therefore the stands can be interchanged very quickly. Different versions including horizontal, vertical, convertible and drop-in-joker (which converts a horizontal to a vertical) are in operation, allowing rapid adaptation to the variety of the rolled products needed to fulfill stringent market demands. Line flexibility allows rolling with low temperature, high alloy, wide forming passes, etc.
Features:
- High competent rigid
- ity Reduced stress path
- Fully automatic operation
- Axial roll adjustment
- Automatic screw- down system
- Possibility for adjustment under load
- A roll balance system, which eliminates backlash
- Minimum wear and positive engagement due to
- self-balancing spindle support Long bearing Life
- Automatic utility connections
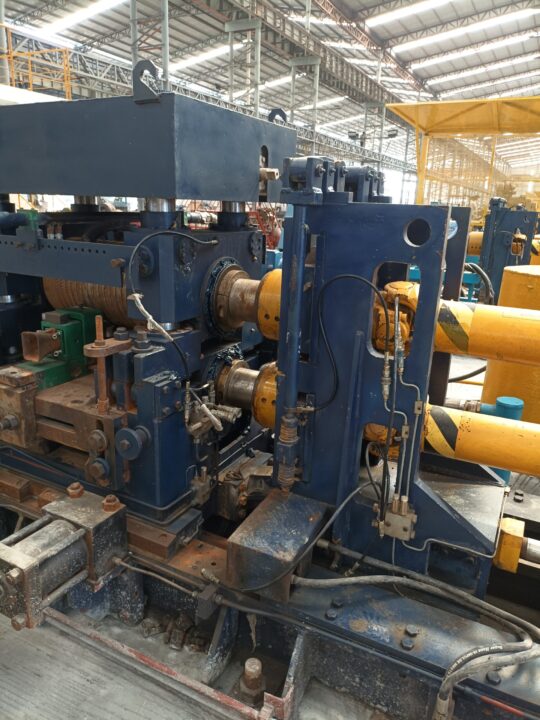
Sliding Stands
Modern 2-high sliding stands are reversible and fully automatic. They represent an innovation solution for roughing and intermediate mills and constitute the latest stage of 3-high stand evolution.
Features:
- A fixed rolling line with sliding stands to match the exact groove according to pass design reduced roller table wid
- th. Advance billet manipulation system.
- Automatic Roll gap adjustment.
- Simple fountains.
- Reduce bite angle due to adjustable entry speed.
Convertible Stands
Today’s mills can be used in a wide range of configurations in order to provide an ultimate selection of products from a single mill layout. It is possible to change from one unrelated product to another by simply pushing buttons and without the lengthy procedures needed for an old style mill change over. Convertible stands allow either horizontal or vertical positioning of the intermediate finishing trains in accordance with production requirements
Features:
- Less than two minutes to change the position
- Excellent stand rigidity
- Reduced foundatain depth
- Quick stand change system without crane requirement
Universal Stands
These stands are interchanged with horizontal stands when rolling structural shapes. In addition to the horizontal rolls, the stands are fitted with a set of idler rolls to work the flanges.
Features:
- Fast stand and roll change Modular design to reduce crane requirement
- Hydraulic vertical and horizontal roll adjustment
- Highest rigidity with housing less design.
In order to meet the enhanced reliability and delivery requirements of the growing industrial applications we have gone for a major expansion and increase in capacity.
We have the required expertise in manufacturing precision gearboxes and have among the best facilities for the entire process. Our team of engineers, metallurgists, modern manufacturing and testing facilities allow us to provide reliability meant for heavy duty.
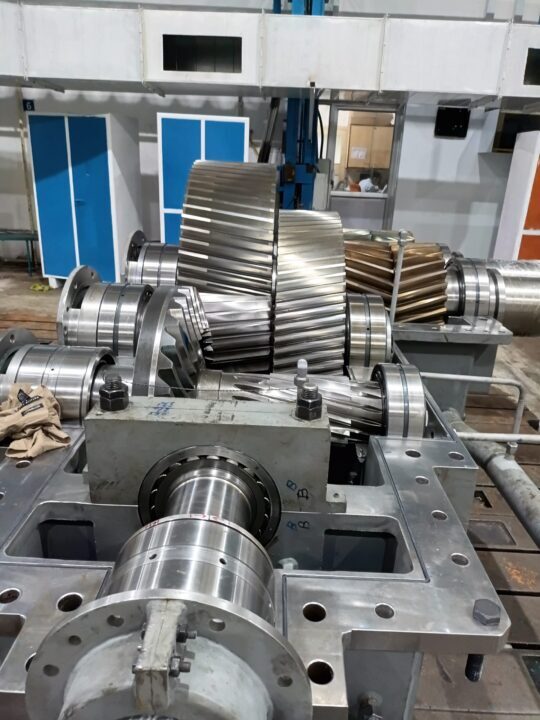
Our passion for manufacturing excellence and commitment to world class quality and on time delivery is clearly reflected in our state of art manufacturing facility spread over 50,000sq.m. including:
- G& E, Libherr and Pfauter gear hobbingmachines
- HOFLER gear grinding machines up to 2000mm and 25 modules
- CNC SCHARMAAN Horizontal Boring machines
- CNC MAAG gear profile testers
- The best names in OD, ID and surface grinding Stress relieving and shot blasting
- KISSOFT based gear designs
- Schenk Dynamics Balancing Machines Sealed
- Quenched Furnace with Sub Zero Facility
- Hand Held Digital Vibration Me
- ter Mitutoyo Model SJ-301Portable Surface roughness Measurement Surftest
Applications
We provide a variety of solutions for:
Product Range
The range of our gear boxes covers the following:
- High Speed Gear Boxes tested up to 10,000 rpm
- Steel Rolling Mills
- Cement Industry
- Sponge iron plants
- Sugar Mills
- Paper Indus
- try Agriculture
- Other diversified industries
- Sequential gearboxes
- Helical Gearboxes
- Planetary Gearboxes
- Bevel Gearboxes
- Over 125 Quenching Systems to produce TMT bars along with flying shears have already been commissioned.
- Quenching Process Solutions in a capacity up to 100 Tons per hour.
- Self-Tempering process that ensures high Weldability
- TMT bars of Fe415, Fe500, fe 550 & fe 600 Grades
- “TEMPCORE” endorsed production process
- Technical partnership with Herbert Roth of Germany
- TMT approved by SAIL and MES
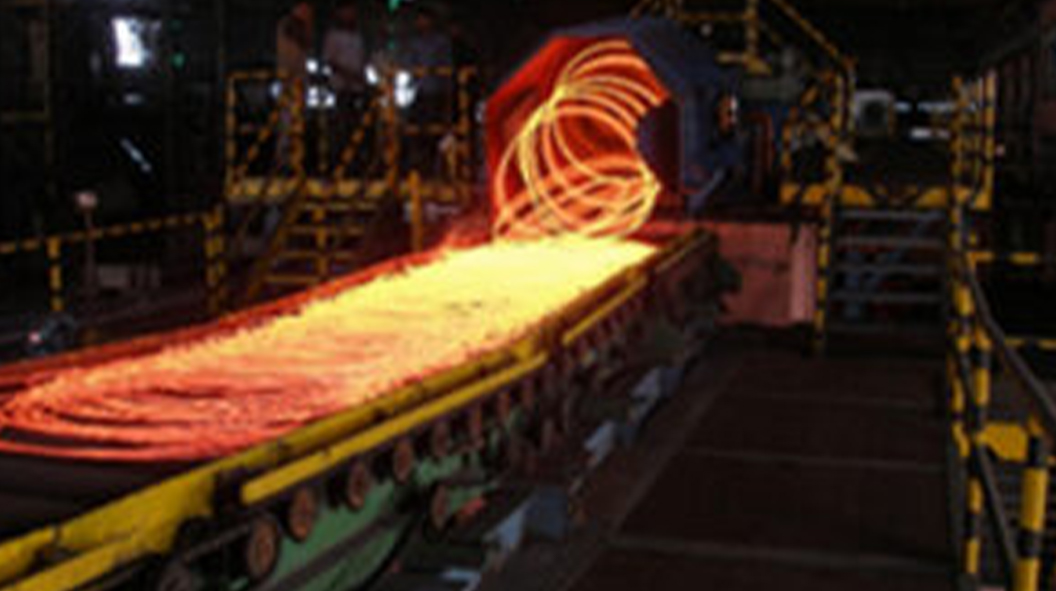
Shears
Crop & Cobble Shear
The Shear are used in Hot Rolling to Crop Front End, Tail End and as well as to segment cutting in case of eventualities. These Shears are start/stop type and are driven either with Flywheel mounted Pneumatic Clutch/Brake or Direct DC motor driven. These shears are controlled through PLC System and provide very close tolerance of the cut length.
Cooling Bed Dividing Shear (TMT Shear)
These Shears are used to cut cooling bed lengths. (Surface Temperature around 350C° min.)These Shears are generally installed after Quenching line & before entry to Cooling Bed.
Shears are Stop/Start and continuous operating type and driven by the Direct DC Motor Drive. These are controlled through PLC system. Hence very close tolerance of cut length is achieved.
Rotary Shear
These cost effective Rotary Shears are used to Crop Font, Tail and as well as to scrap the pre quenched bars during emergency. These Shears are continuous rotating type. Generally these Shears are used to trim Hot Rolled Bars at considerably at lower speed.
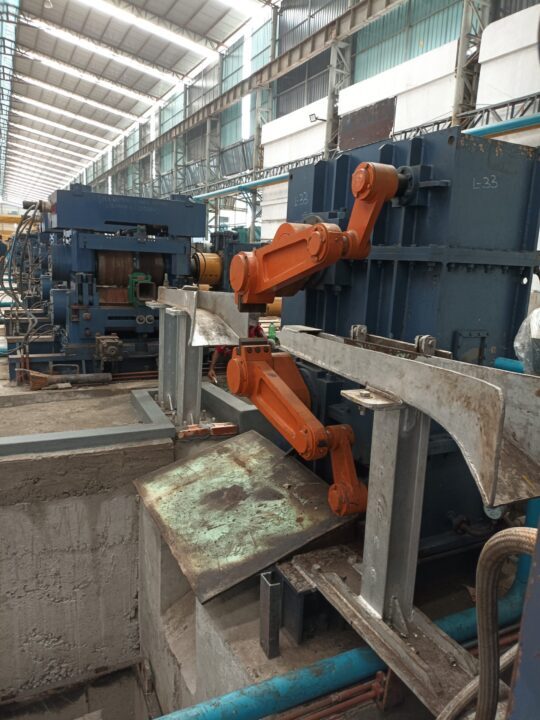
Hot Saws
These Hot Saws are used in hot rolling to cut desired length and as well as top trim Front & Rear End. These shears are capable are capable of cutting section size ranging from 80 to 600mm(Beam, Channel, Angle) and as well as Square, Rounds of 40 to 250mm. These Hot saws presently are two types: Pendulum swinging type and horizontal shift type.
Cold Saws
PPRM designs flying and static type cold shears, with clutch and brake or direct drive, to produce the ultimate and product.
Features:
- Both open & closed types are available.
- Extremely precise cutting.
- Quick change device for blade replacement.
- Handles quenched rebar and high alloy steels.
- Available with start stop drive.
Salient Features
High rigidity, reliability and quick roll change capabilities are the key features of the state of the art mill stands, which are designed for producing bars, wire rod, angles, channels, and universal beams. The connection and disconnection of the spindles and all the fluid utilities are fully automatic and therefore the stands can be interchanged very quickly. Different versions including horizontal, vertical, convertible and drop-in-joker (which converts a horizontal to a vertical) are in operation, allowing rapid adaptation to the variety of the rolled products needed to fulfill stringent market demands. Line flexibility allows rolling with low temperature, high alloy, wide forming passes, etc.
Design Element
- Rigid & compact design
- Canti-levered rolls
- Rolls placed in 450 planes with 900 stand to stand orientation
- Neck diameter of 150mm.
- Modular design .
- No-Twist feature.
- T.C. Rolls
- cobble block and snap shear.
- Emergency oil supply tank.
- Oil and water separator.
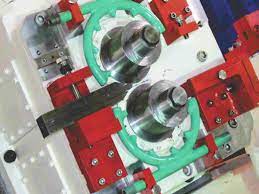
Benefit Delivered
- Consistency in product size /tolerance Operator friendly /ease of change over.
- Ease of roll changing,
- Allows rolling of product size as high as 20mm. Diameter.
- Interchangeability of cassettes
- Lesser incidence of cobb
- le. Super finish bars.
- Safety of T.C. Rolls .
- Saftey of bearings and gears in case of power failure.
- Supply of clean oil.
Cooling beds naturally cool the material as well as cross transfer towards the discharge end. PPRM cooling beds are designed using standard elements that can be combined in accordance with plant product mix requirements and production capacity.
Full mechanical component standardization assures constant equipment quality, as well as high performance levels. Depending on differing speed requirements, cooling beds are entry can be completed with lifting aprons and natural braking, magnetic braking, or twin channel and mechanical braking. For special applications, the cooling beds are provided with slow cooling by insulated covers and forced cooling by water spray systems or water tanks. A twin or double twin channel system for extremely high rolling speeds is available.
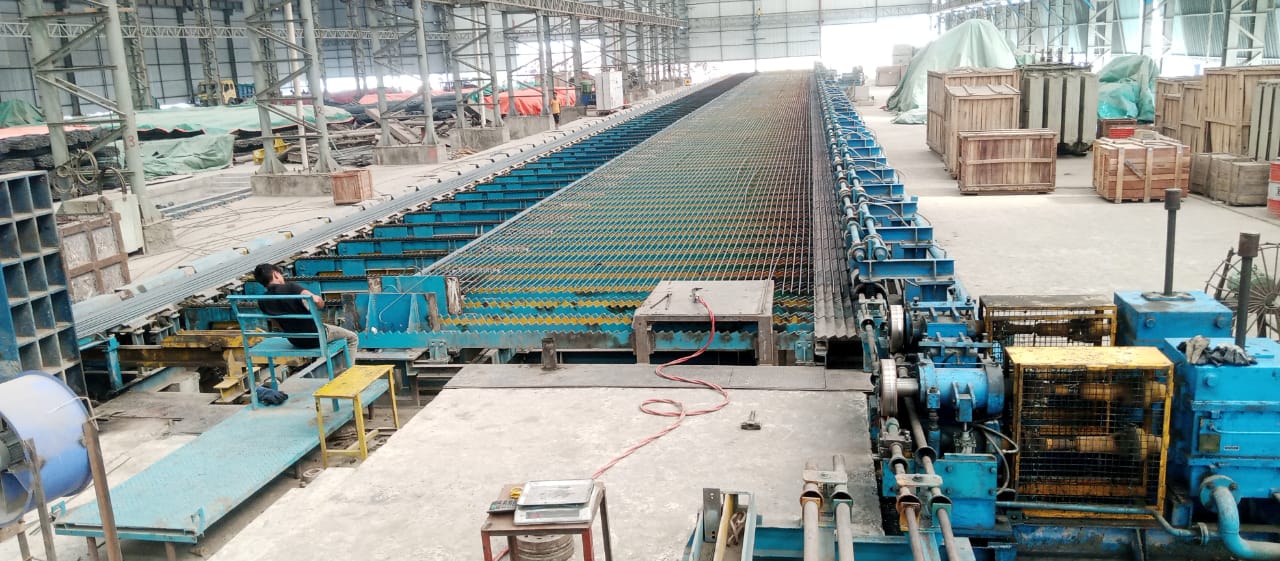
These types are:
- Automatic rake type cooling bed which transfers the material by one pitch for every rake movement. These are provided with twin channel bar delivery system or run in table with apron type diverters. The bed is provided with bar alignment.
- Turn over type cooling bed for alloy steel which rotates the bars by one revolution every time the rake moves by a pitch. These impart superior straightness in material improvised metallurgical properties as the bars are uniformly cooled.
The twin channel offers solution to bar handling at cooling bed at high speeds. Twin channels are available for bar sizes up to 40mm in India and stock speeds as high as 30meters per second. This carries the bar in a closed channel until the material comes to a standstill position and discharges it to the bed below automatically.
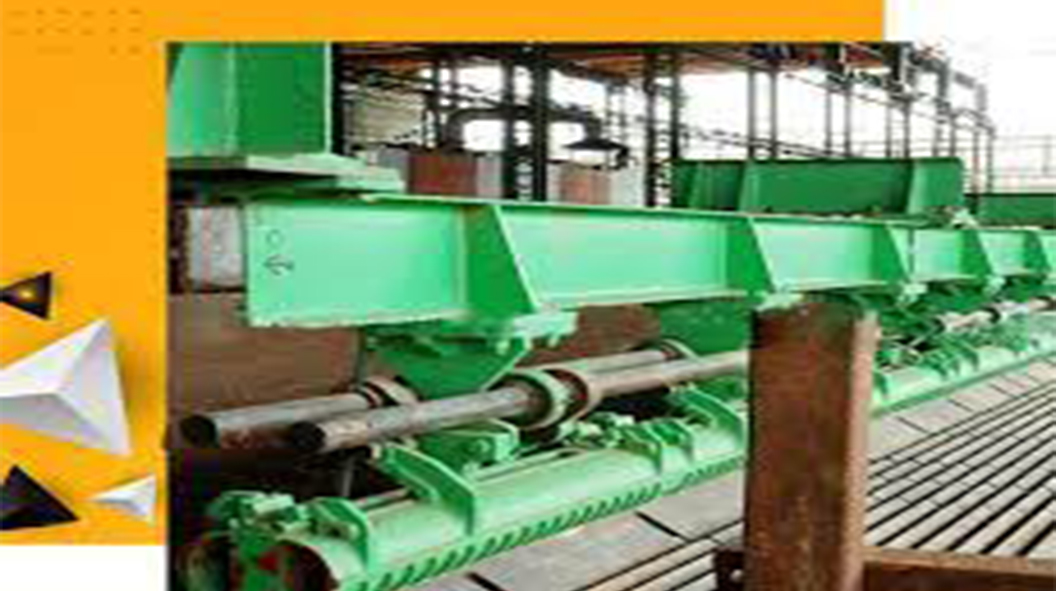
This is an excellent system as it carries the bar in a closed channel, minimizing the accident hazards. Specifically while carrying out high speed rolling the system is an absolute necessity.
Its design features makes it possible to work in conjunction with braking pinch rolls, minimizing the length of run-in. The operations of twin channel are automated and are guided by the discharge of the rods from dividing shear. An innovative idea for cast iron center boxes has drastically brought down maintenance time.
Coilers are of Edenbourne and Garret type forming the coils with coil axis vertical. The coilers are available for rod sizes from 5.5mm to 50mm and bar speeds up to 40m/sec.
The design is compact and rugged. The laying pipes are so configured to obtain the output coils of perfect shape. Bearings are protected heat radiations.
- High competent rigid
- ity Reduced stress path
- Fully automatic operation
- Axial roll adjustment
- Automatic screw- down system
- Possibility for adjustment under load
- A roll balance system, which eliminates backlash
- Minimum wear and positive engagement due to
- self-balancing spindle support Long bearing Life
- Automatic utility connections
Features:
Wide range of applications, including heavyweight and large coils
Improvements in coiling capacity and coil shape
- Two special poring pipes for large rods and small wires. The large pouring pipe is equipped with pinch roller at one end (Japanese patent pending). The small one can adjust pouring angles and telescopic lengt
- hs. Ideal wave shapes, due to complete wobbling control during coiling machine rotation.
Prevention of defects on coils
- Inside reel pins retract when unloading coils (Japanese patent 729368).
- Coils can be handled without sliding them on the machine (Japanese utility model 1003805)
Stable Coil transportation
- Coil hold devices for coil turner and double-plate conveyor (both Japanese patent pending).
- Prevent coils from sliding and falling.
Bar Handling Area
Finishing equipment includes the automatic staking, bundling, binding, weighing and labeling of rolled products.
Stacker and building Systems
All stackers have a built-in bundling function. Bundlers for round and flat bars available together with bar counting for rounds and small bundle processing systems.
Stackers suited to handling straight and reverse layers are available for all type of sections. Handling of the straight and reverse layer can be mechanical or magnetic or magnetic with high stacking cycle performance.
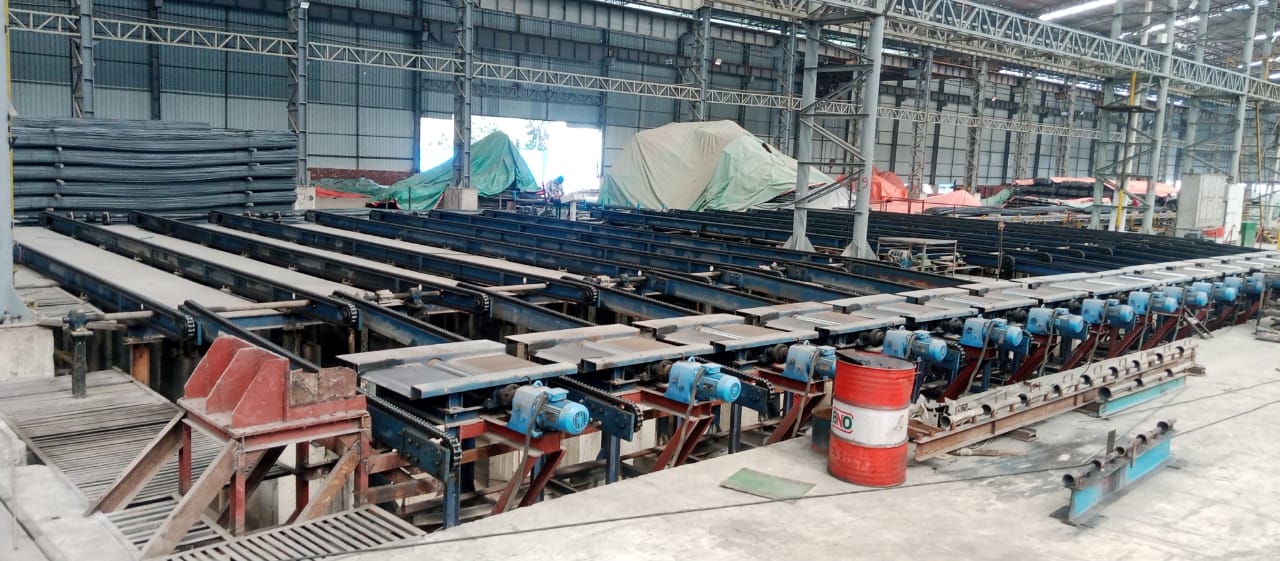
The packing form can be round, square, rectangular and hexagonal.
Binding Systems
Automatic binding of the packages and bundles is available with wire or strapping.
Weighing & labeling
All bundles can be automatically weighed and further labeled for quality assured delivery of the finished products.
Tailor made to customer design and specifications for Steel/ Tube/ power/ sugar/ chemical plants.
“Cost Effectiveness” of an equipment builder would greatly depend on his in-house facilities and man power competence, which in the ultimate analysis, would determine Quality of equipment and timely delivery.
Complete infrastructure and machines are available in-house in 100000 sq.m. of work space, to handle wide range of jobs and tasks. We also specialize in machining of heavy jobs on Horizontal Boring, Vertical Borings, Gear Hobbings to name a few. These machines are well supported by EOT cranes with a maximum capacity of 40 Tons having a lift of 8.5m. Our facilities are backed by 100% stand by emergency power supply.
Satisfied customers include industry leaders like Larsen & Toubro ltd.& TISCO growth shop for Steel Plant and Bulk Material handling Equipment, Flovel Hydro ltd. And Andritz for Power Plants, Mecon & Flat products (l) Ltd. For Cold Rolling Mills, Krupp (India) Ltd. For Sugar plants, Siemens VAI & Danieli for Steel plant equipment.
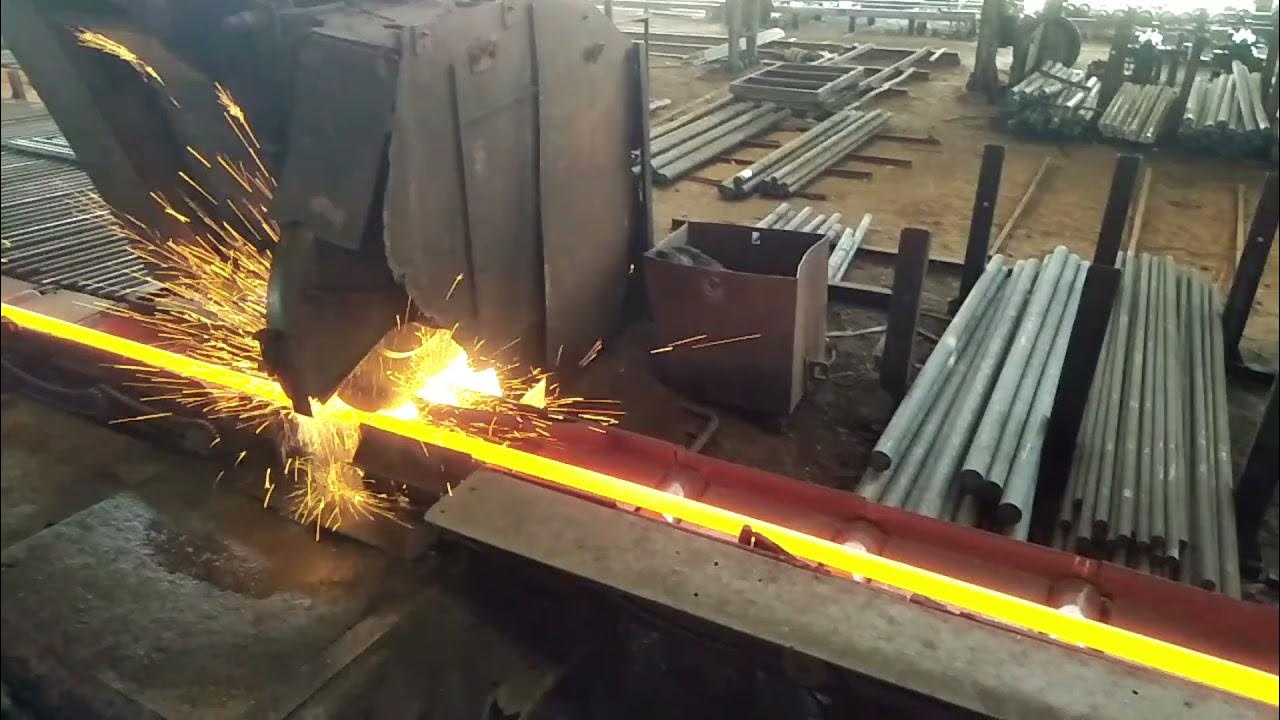
Sliding Stands
Modern 2-high sliding stands are reversible and fully automatic. They represent an innovation solution for roughing and intermediate mills and constitute the latest stage of 3-high stand evolution.
Features:
- A fixed rolling line with sliding stands to match the exact groove according to pass design reduced roller table wid
- th. Advance billet manipulation system.
- Automatic Roll gap adjustment.
- Simple fountains.
- Reduce bite angle due to adjustable entry speed.
Convertible Stands
Today’s mills can be used in a wide range of configurations in order to provide an ultimate selection of products from a single mill layout. It is possible to change from one unrelated product to another by simply pushing buttons and without the lengthy procedures needed for an old style mill change over. Convertible stands allow either horizontal or vertical positioning of the intermediate finishing trains in accordance with production requirements
Features:
- Less than two minutes to change the posit
- ion Excellent stand rigidity
- Reduced fountain depth
- Quick stand change system without crane requirement
Universal Stands
These stands are interchanged with horizontal stands when rolling structural shapes. In addition to the horizontal rolls, the stands are fitted with a set of idler rolls to work the flanges.
Features:
- Fast stand and roll change Modular design to reduce crane requirement
- Hydraulic vertical and horizontal roll adjustment
- Highest rigidity with housing less design.
High rigidity, reliability and quick roll change capabilities are the key features of the state of the art mill stands, which are designed for producing bars, wire rod, angles, channels, and universal beams. The connection and disconnection of the spindles and all the fluid utilities are fully automatic and therefore the stands can be interchanged very quickly. Different versions including horizontal, vertical, convertible and drop-in-joker (which converts a horizontal to a vertical) are in operation, allowing rapid adaptation to the variety of the rolled products needed to fulfill stringent market demands. Line flexibility allows rolling with low temperature, high alloy, wide forming passes, etc.
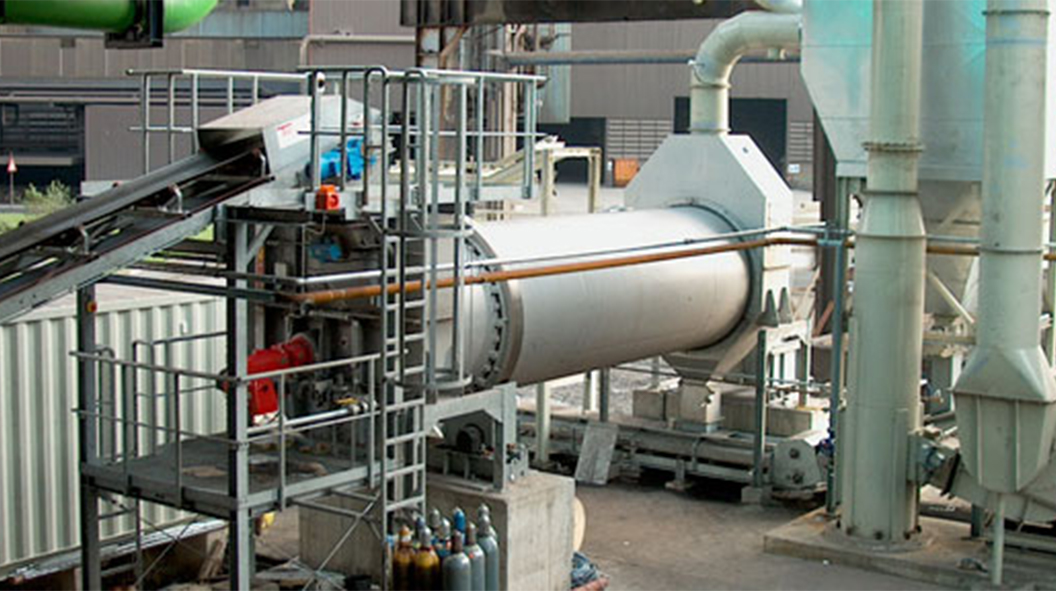
CNC Roll turning Lathe
- Siemens 802D CNC controller with 0.001 resolution .
- 1100mm width 4guideways bed for better rigidity .
- Large size spindle bore and heavy duty tail stock .
- Hardened and ground guideways with Turite-B for longer life
CNC Roll turning & CNC Roll Notching
- Single Machine that does both Roll Knurling and name Engraving.
- Swivel head for accurate name engraving.
- Fly milling head for smooth Knurling SIEMENS.
- CNC controller with easy to use software.
- All international rolled ribbed bars standards can be engraved